Manufacturing Support
Optimal Manufacturing Support
We are experienced in all aspects of metal processing and has a wide networking base of suppliers and sub-contractors. Therefore, we are able to meet customer’s requirement with different types of processing methods and propose the best method to achieve customer’s specification.
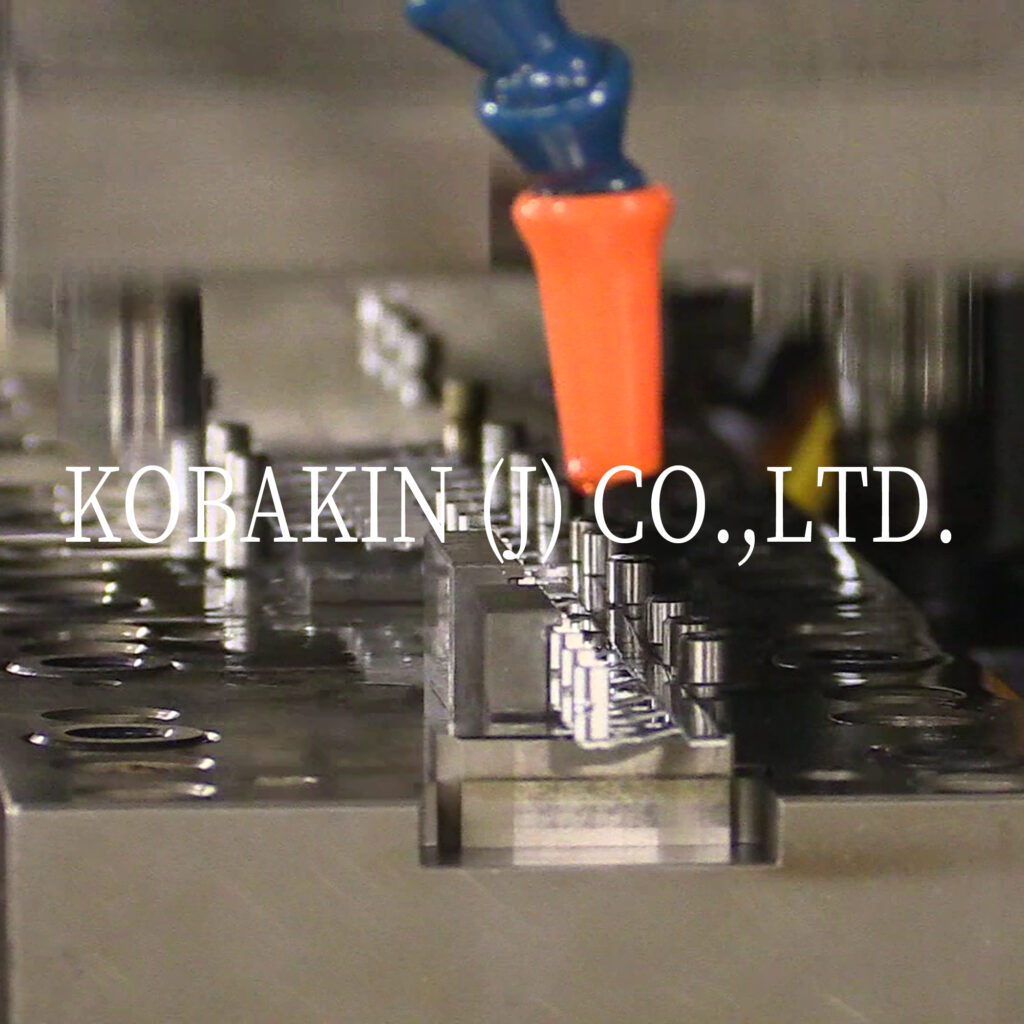
Prototype Development Support
We can support customer in development by involving in product concept stage. We could fabricate soft tools for R&D purposes. Through prototype trials, we analyze, evaluate and propose the optimum shape or design toward long term mass production. In addition to soft tool production, we could also apply V-bending and metal spinning for small quantity trials. Thus, we are able to meet the development needs of our customers with low cost and short delivery time.
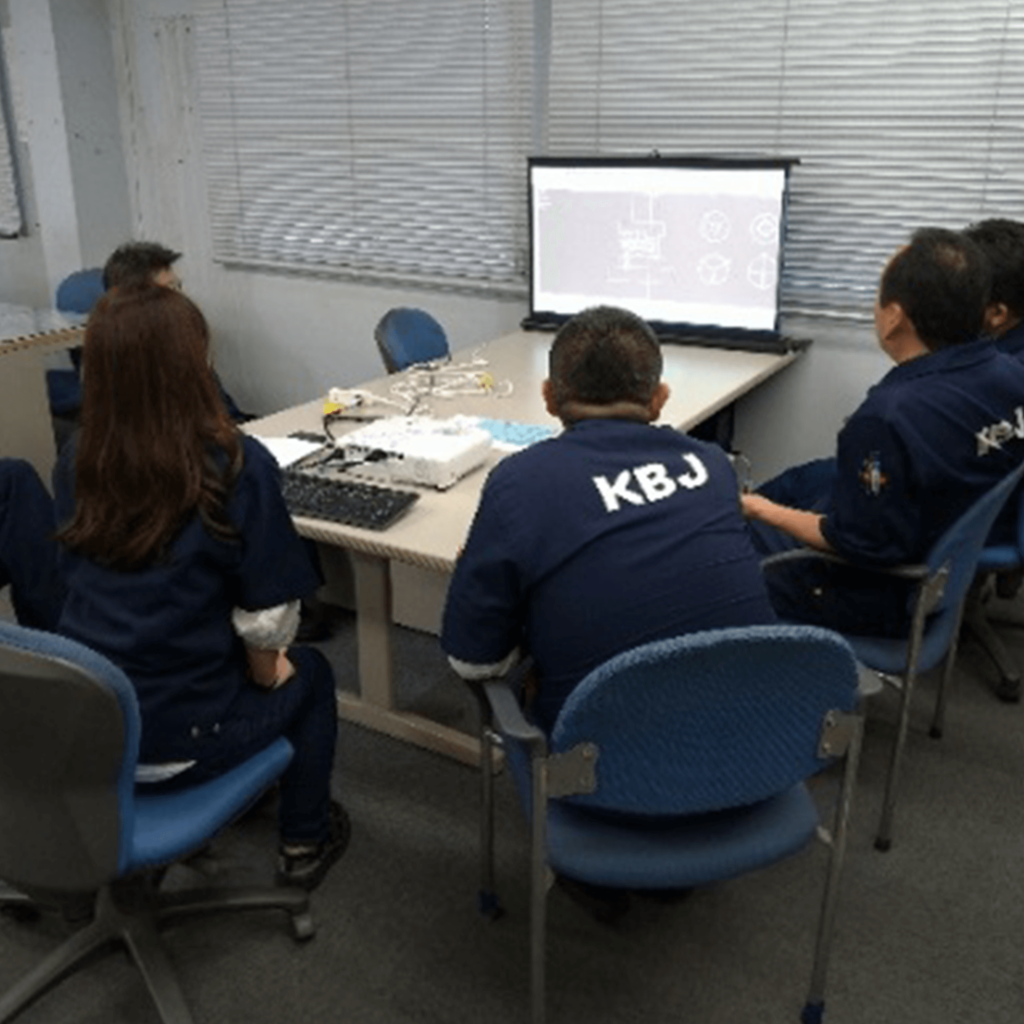
Quality Assurance Support
We provide highly reliable quality with technical capabilities and quality assurance system cultivated from years of manufacturing high performance vacuum tube parts used in medical, analyzers, satellite and defense communications. We are equipped with precision measuring devices such as CNC image measuring system and image dimension measuring system. We also provide reliability by visual inspection using microscope and magnifiers. In addition, we support various component analysis and environmental tests.
-2-1024x576.jpg)
Press Stamping from Cutting Work
~ Achieving significant cost reduction ~
This part was originally manufactured by cutting, but its unit price is very high and cost reduction has been an issue for many years. Therefore, we utilized drawing and burring press technology, and finishing with tabletop lathe, and thus, significant cost reduction were achieved.

Ingenuity of Tooling Designer & Engineer
Due to the requirement of burring process at the side of the part and the step drawing shape at the upper and lower parts, it is a challenge designing the tooling and various experiments were carried out before tooling fabrication. After that, I adjusted the tooling several times to improve the dimensions and processing accuracy. It is also difficult to achieve the round shape of the body.
Production Efficiency Improvement
~ Significant productivity improvement & cost reduction by automation ~
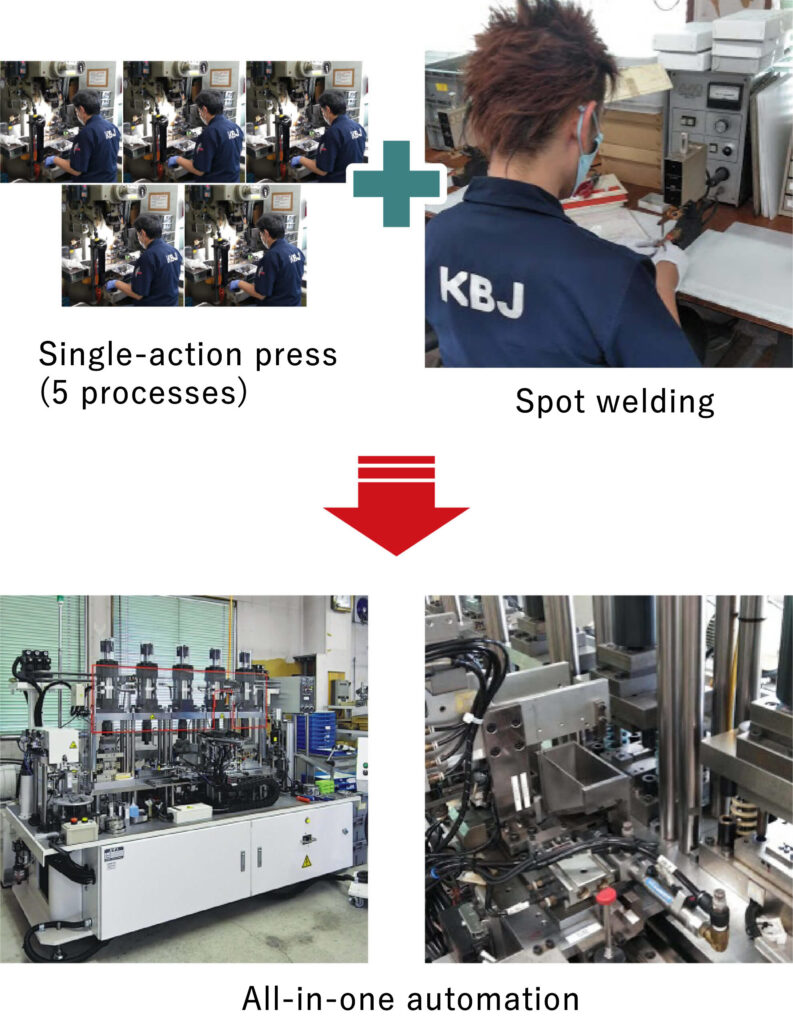
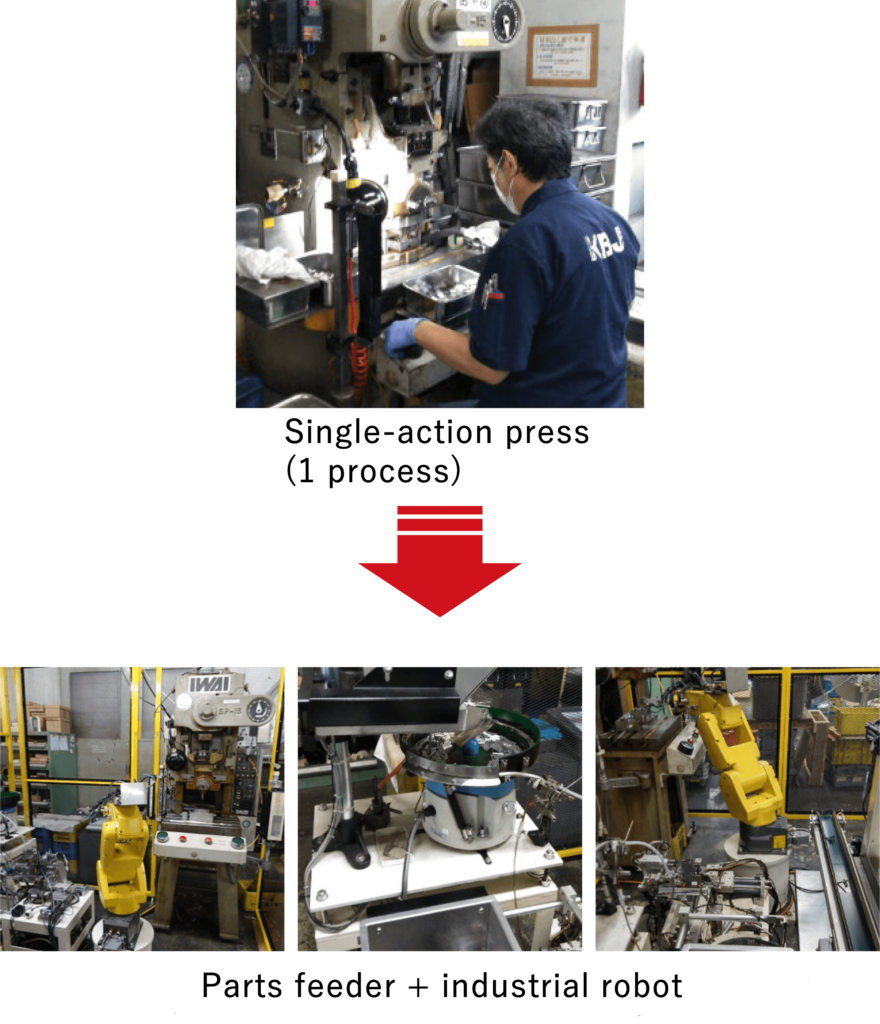
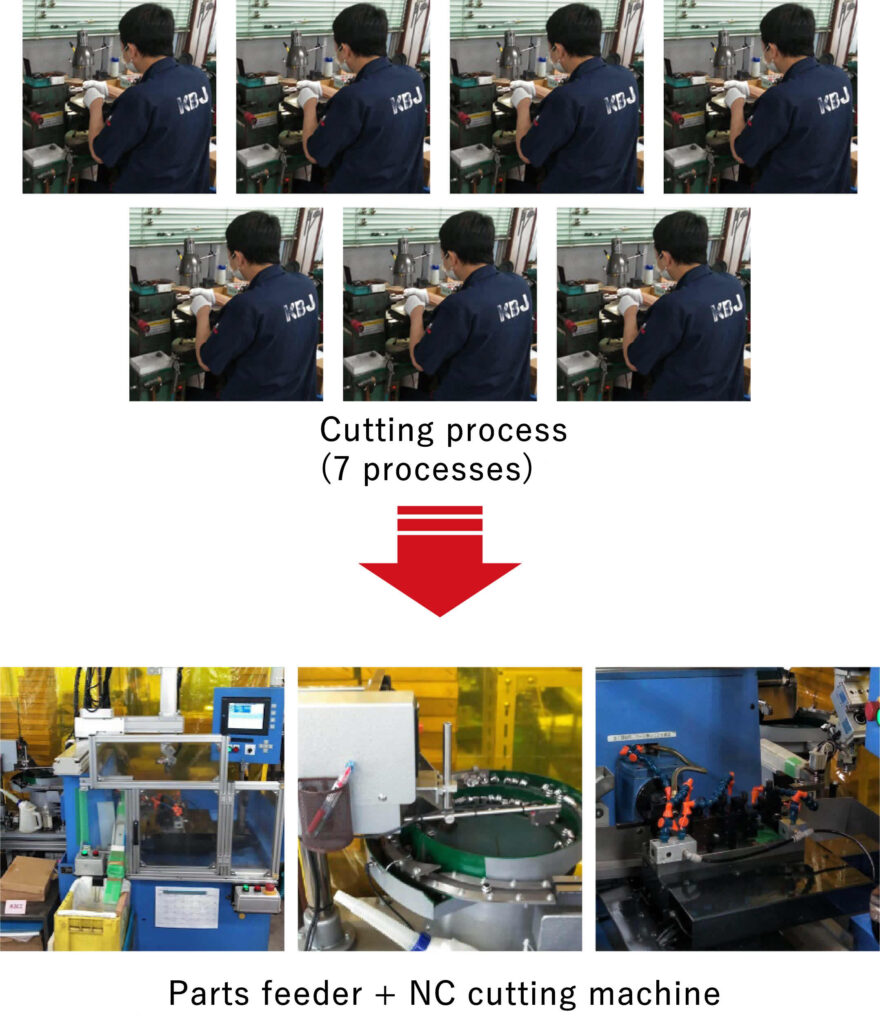
Alternative Material Proposal
~ Propose VE and appropriate materials from prototype stage ~
Case Study 1: Customer request
As a jig for parts that form a film in the semiconductor pre-process, the side surface of the plate is used. How do I ensure plate thickness tolerance is within 0.02?
Material Spec: SUS304 - t0.323 +0/-0.02
Proposed precision rolling
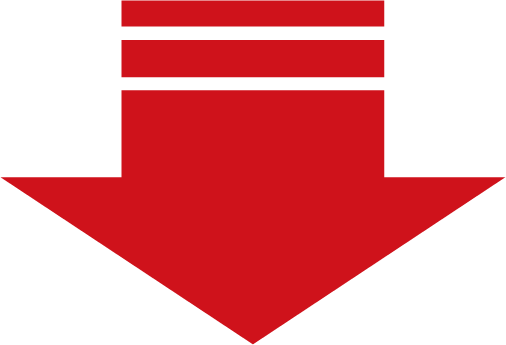
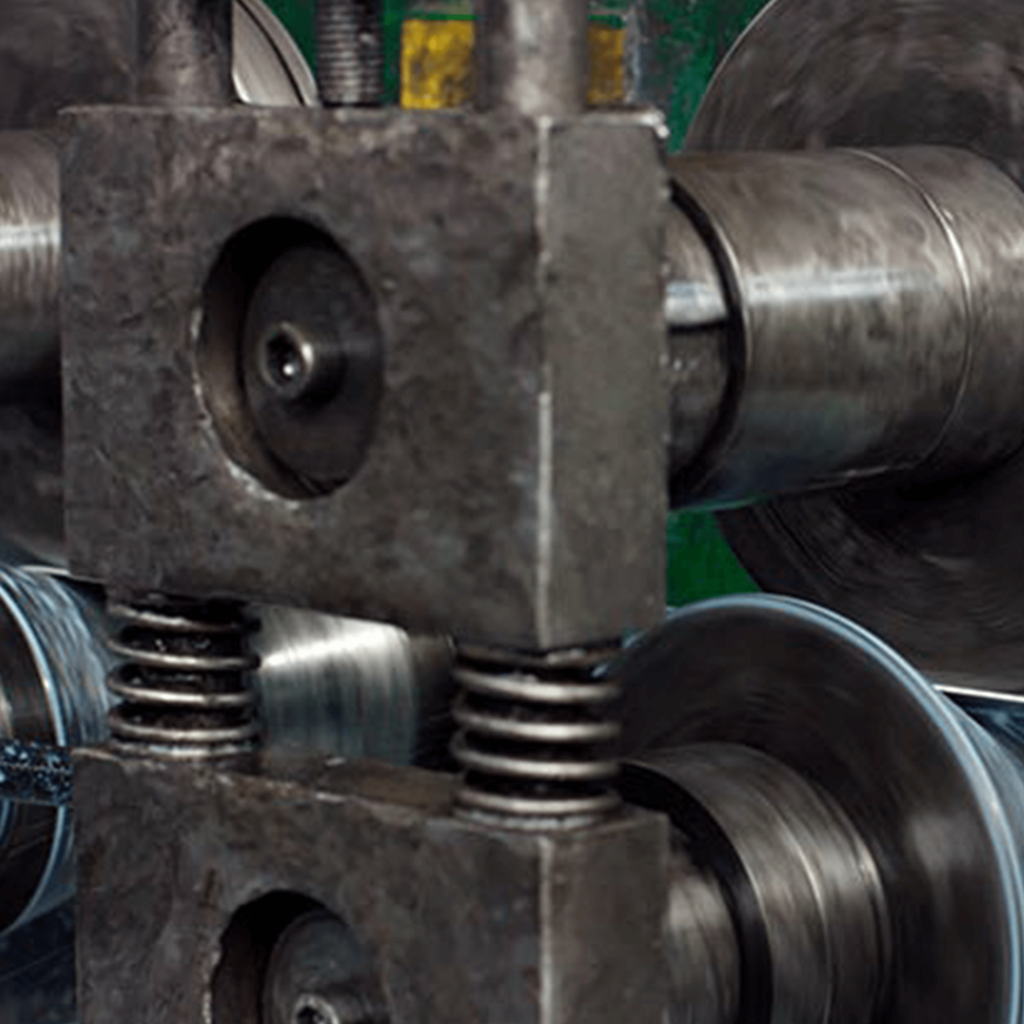
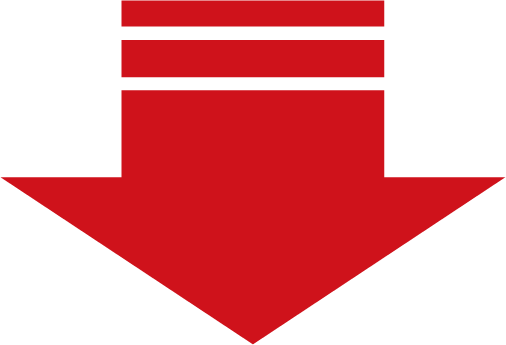
Achieved desired tolerance
Case Study 2: Problem encountered
Drawing Spec: SUS301 CSP-1/2H
There is a problem with the workability of the material as it resulted in cracked parts during processing, low tooling durability and deteriorating productivity. I was asked for improvement measures.
Proposed material change - SUS304 CSP-3/4H
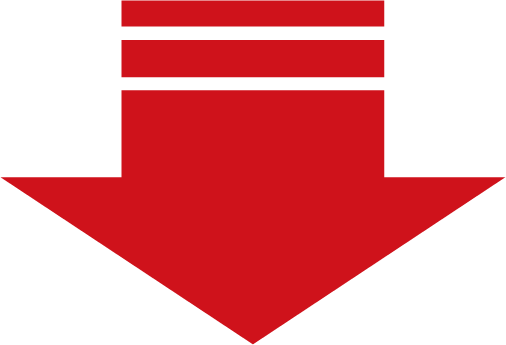
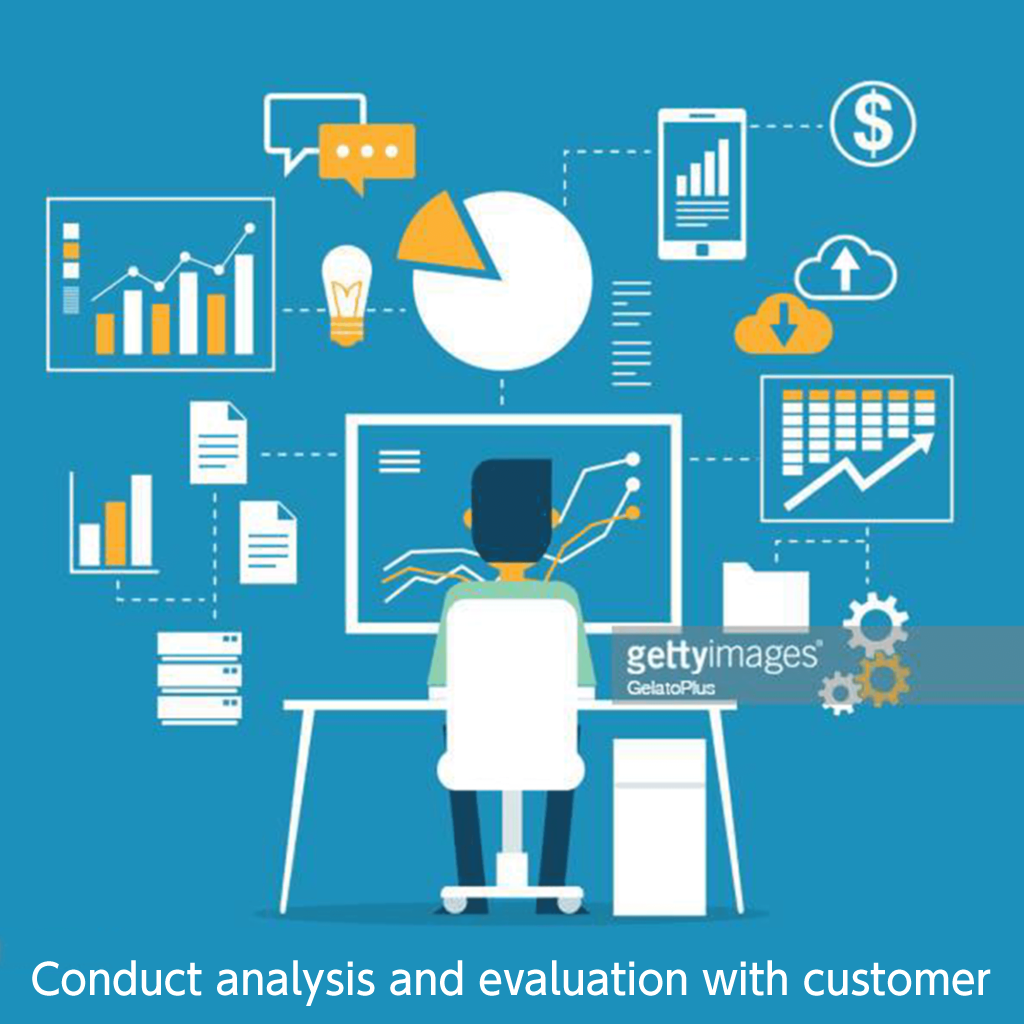
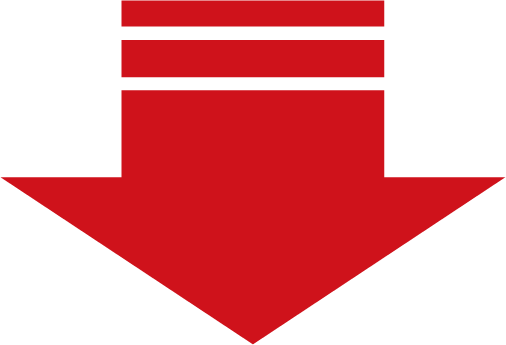
Improved parts quality & tooling durability
Contact
Please feel free to contact us using the Inquiry Form.